Manufacturing Process Guide
Manufacturing Process Guide

Die Casting
Description
Molten metal is forced into a die using pressure.
Common Materials
Nonferrous metal alloys- Aluminum Alloys, Magnesium Alloys, Zinc Alloys
Advantages
High productivity, economical for high volume production, good mechanical properties, part to part consistency, good dimensional tolerance [1]


Injection Molding
Description
Plastic pellets are melted then forced into a die using pressure.
Common Materials
Thermoplastics- ABS, Polypropylene, HDPE, LDPE, PVC, Nylon, Acrylic.
Advantages
Detailed features and complex geometry possible, multiple plastics can be combined, fillers can be added to change properties, high efficiency.


Investment Casting
Description
Pattern is covered in a ceramic slurry, then burned out after the slurry dries. Molten metal is poured and the mold broken.
Common Materials
Most ferrous and nonferrous metals- Carbon, tool, and stainless steel. Aluminum, magnesium, copper based alloys.
Advantages
Great surface finish and no parting line, can be used for complex designs can include undercuts, can make parts a machine (mill or lathe) can't.

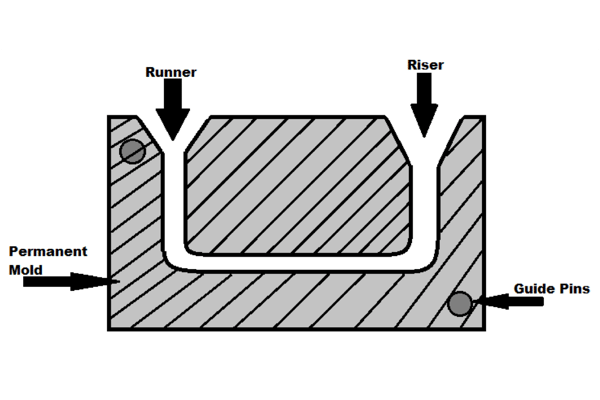
Gravity Casting
Description
Molten metal is poured into a reusable, permanent mold, using gravity to fill the mold cavity.
Common Materials
Aluminum, magnesium, copper alloys and zinc alloys. If a graphite mold is used, iron and steel can be cast this way.
Advantages
Smooth surface finish, good dimentional accuracy, fast production time, can make parts with internal pockets using sand core inserts, low scrap rate.
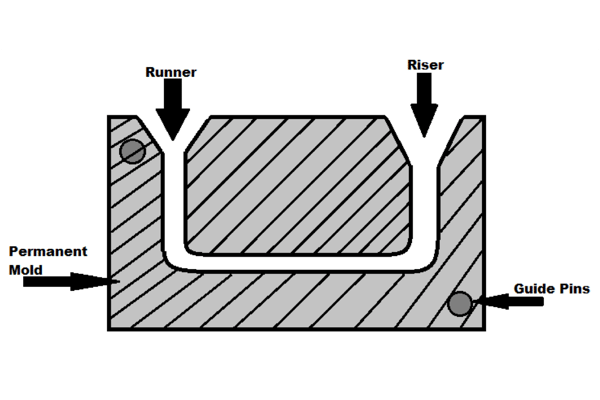
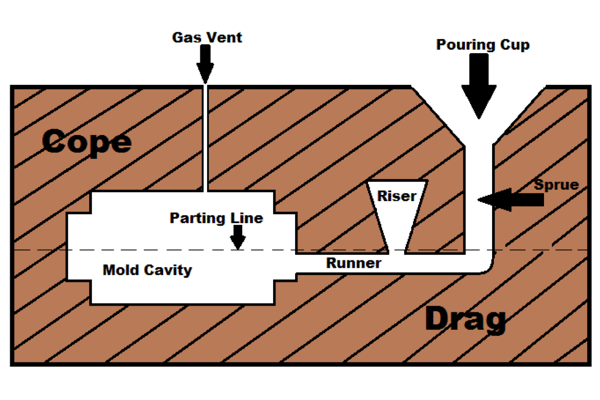
Sand Casting
Description
Sand is packed around a reusable pattern to create a mold. Molten metal is poured and the mold is broken to remove the part when cool.
Common Materials
Iron, brass, bronze aluminum alloys.
Advantages
Least expensive option for small volume production, can be used to make large parts, low post-casting tool cost, sand is reusable.
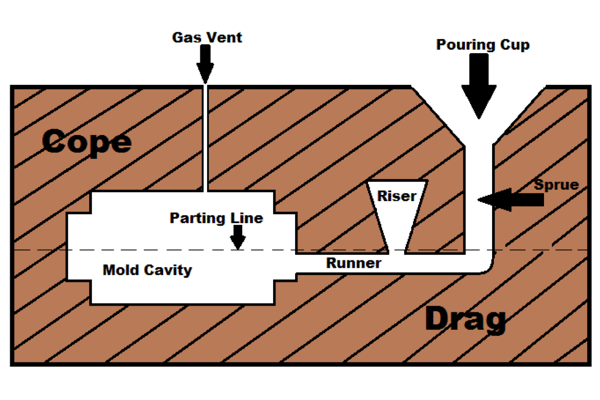
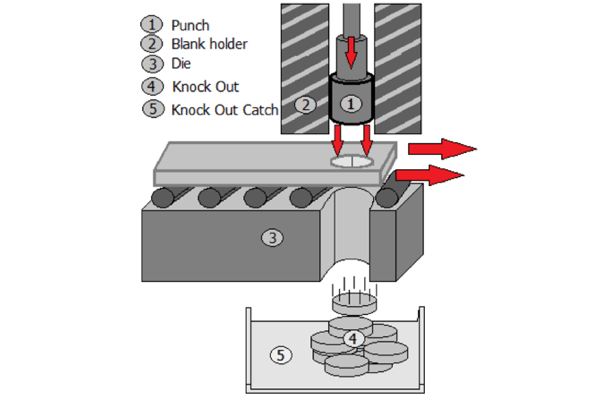
Stamping
Description
Dies and punches are used to cut, bend, and stretch sheet metal to create the part.
Common Materials
Cold rolled and stainless steel, brass copper and aluminum.
Advantages
Repeatablility and part to part consistancy, fast cycle time, low cost per part.
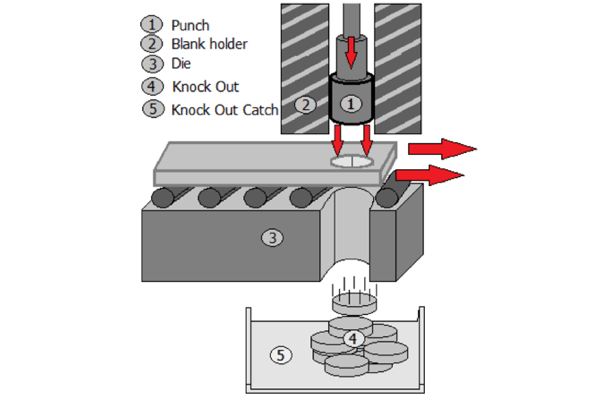

Sheet Metal Bending
Description
Sheet metal is bent into the desired shape either with or without a die. Bends can be on edges or in the middle of the sheet.
Common Materials
Sheet metals.
Advantages
Sheet thickness maintained, variety of angles and geometries possible, good repeatability.


Forging
Description
Heated billets of metal are shaped through hammering between two dies.
Common Materials
Carbon, alloy and stainess steels. Aluminum, titanium, brass, copper and high temperature alloys.
Advantages
Great control over mechanical properties because of control of grain growth, flexible for many different sizes, shapes, and materials.


Extrusion
Description
Heated metal is forced through a die to create rods, pipes, or profiles of a new cross-section.
Common Materials
Aluminum, zinc, magnesium, copper.
Advantages
Continuous, efficient high volume production, low cost per pound, large variety of cross-sections possible.
